Story
As a start-up 3D printing company founded in 2020, EIBOS believes in the core values embodied in our name - Excellent Ideas Based On Structures. Our goal since inception has been to develop products that can truly benefit users through an approach focused on research, exploration, and data-driven decision making.
From our perspective, we are not only a 3D printing equipment manufacturer, but also a user of 3D printing technology and a member of the 3D printing community.
Nowadays, high-speed 3D printing has significantly impacted the industry and expanded the range of applications. After we extensively evaluated many existing extruders on the market, we found that most of them are unable to deliver the performance necessary for truly high-speed 3D printing, especially when working with flexible filaments. This led us to develop the Artemis, a new 3D printing extruder designed to address these challenges.
Artemis is compact and lightweight, reducing the weight of the entire extrusion assembly. It utilizes a 15:1 gear reduction ratio to provide robust extrusion torque required for high-speed printing. A specially designed extrusion mechanism improves the fast printing of flexible filaments. In addition, the transparent cover allow for direct visualization of the extrusion process. In the mean time, customizable rotation axes add an interactive element that enhances the user experience.
With its launching, Artemis aims to expand the possibilities of high-speed 3D printing. It is tailored for complex materials previously difficult to print at higher speeds. We believe Artemis can help further our mission by enabling effective high-speed production across an even broader range of material selection and applications!
The Artemis extruder was designed for high speed, capable of functioning as either a direct or remote extruder. Its specialized gearing and elastic extrusion mechanism can accommodate a wider variety of filament types. This adaptability helps meet the diverse needs of users across different materials.
The Artemis extuder can be easily integrated with multiple hotend configurations. Installation simply requires modifying firmware parameters like E-axis step value and current for the E-axis driver. The Artemis extuder also suitable for 3D printers that support editing firmware settings.
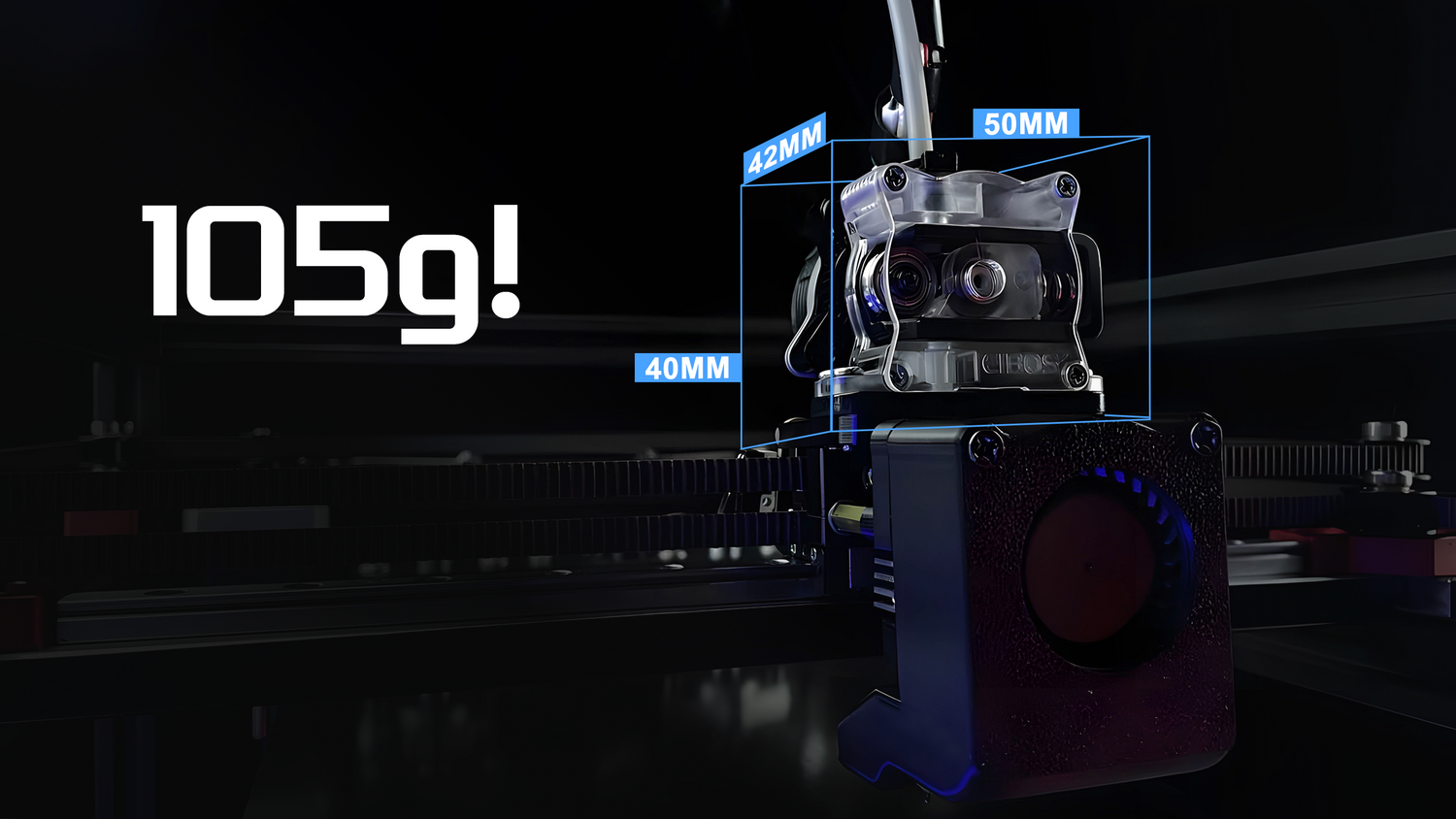
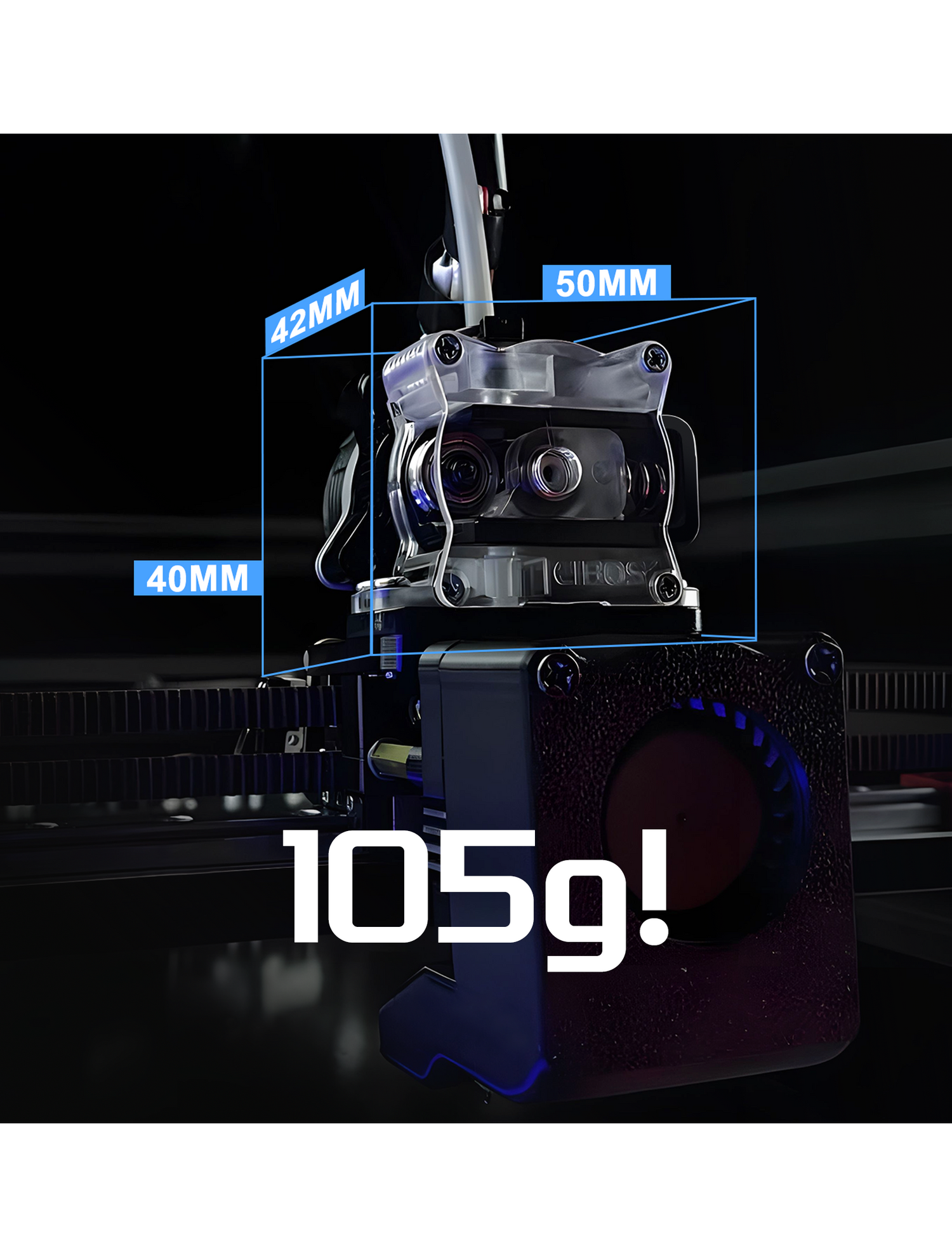
105g! Small size!
The Artemis utilizes a customized stepper motor. It is compact yet delivers high torque output. Combined with long-term durability and resistance to elevated temperatures, this motor powers precision extrusion at high speeds.
The whole design keeps the entire extruder assembly remarkably light at just 105g. This extremely low moving mass enables faster printing while reducing mechanical stresses on printer components during operations. The compact and lightweight Artemis can significantly cut down on inertia on the X-axis.
Pairing the lightweight extruder with a high-flow hotend allows for rapid material flow. This facilitates high-speed printing without compromising quality. By minimizing mass on the X-axis and optimizing material throughput, the Artemis delivers a notable improvement in maximum print speeds and positional accuracy across the entire printer.
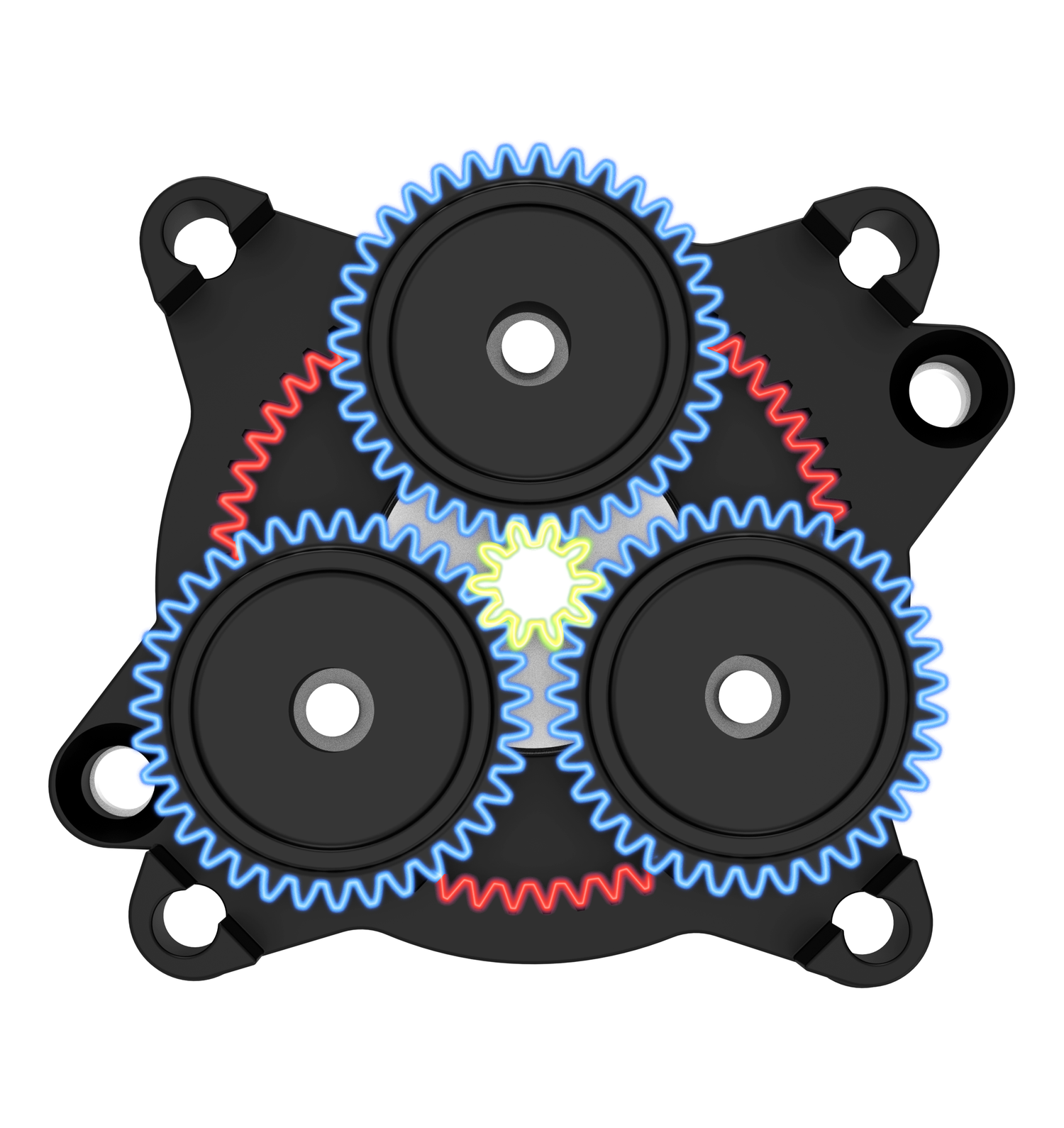
1:15 Reduction ratio
The gear reduction ratio can effectively increase the extrusion torque. The Artemis features an optimized NW-style planetary gear train to significantly boost torque output.
At the center is a 10-tooth sun gear driven directly by the stepper motor. Surrounding it are 3 planet ary gears , the planetary gear is divided into two layers, one with 15 teeth and one with 35 teeth. Which then engage a stationary 60-tooth ring gearforming the casing.
This innovative duplex gearing arrangement results in a big torque multiplication factor. Artemis generates sample extrusion torque for continuous, high-volume deposition even at heightened printing velocities.
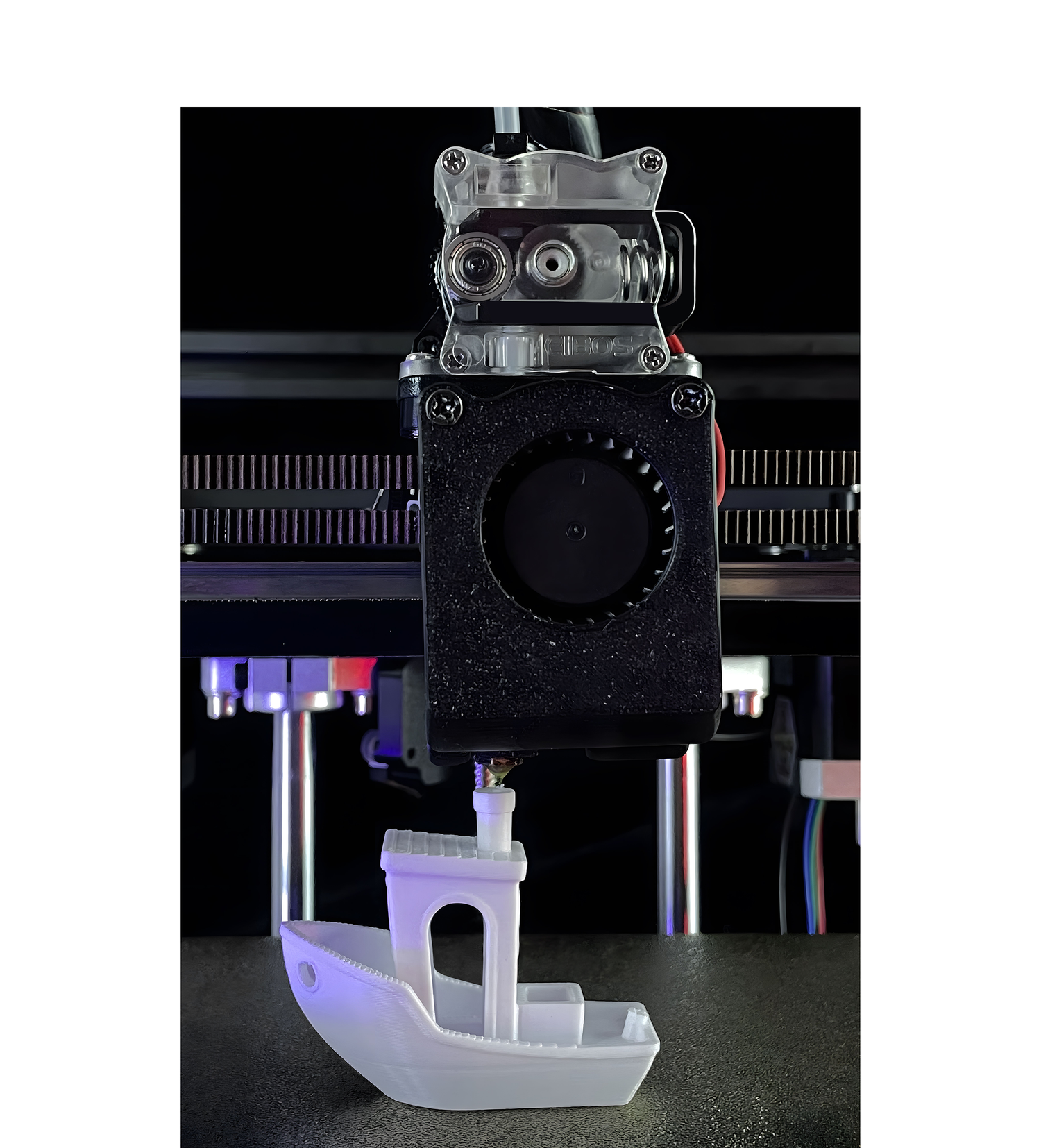
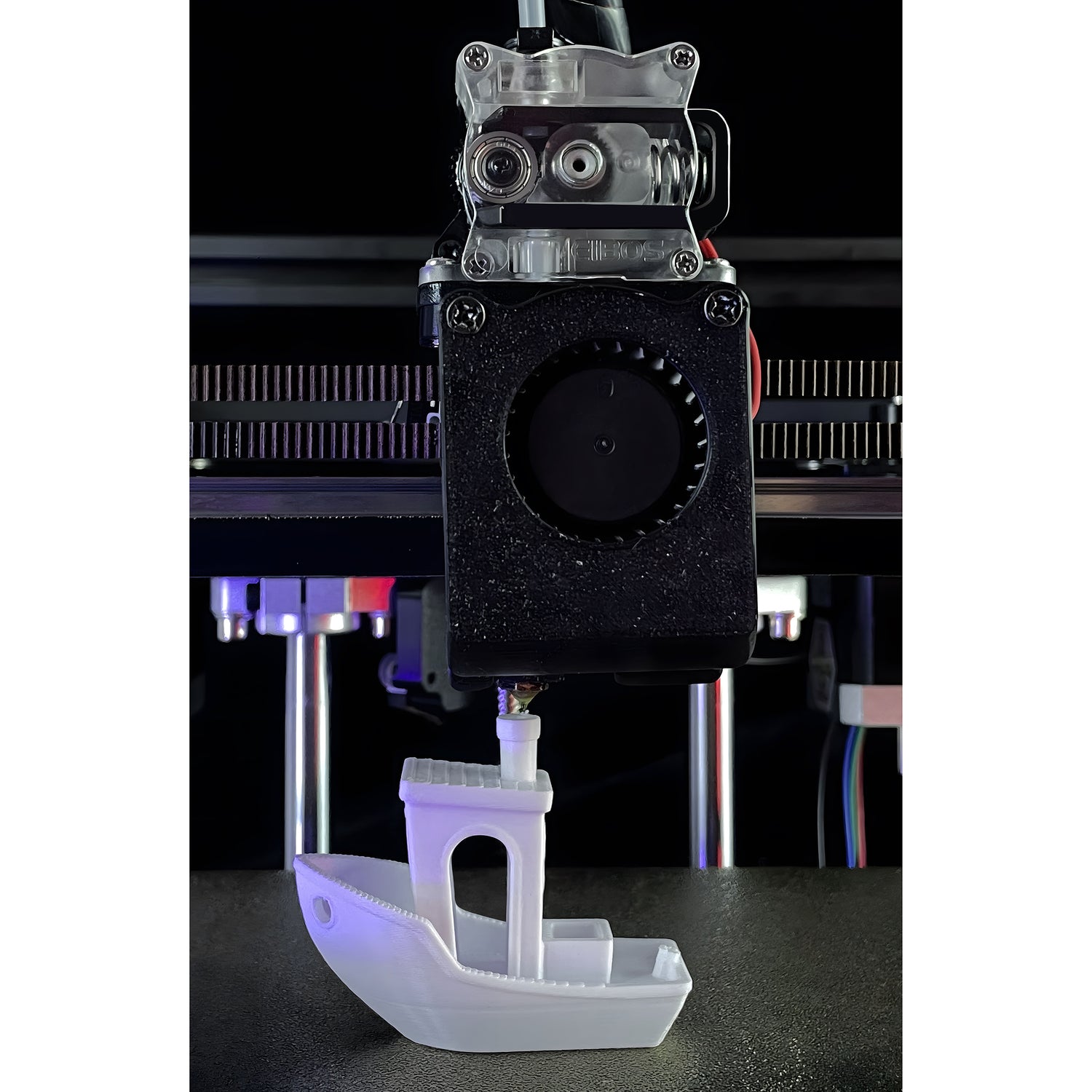
Fast flexible filament (85A) extrusion
‘30min a 85A Benchy.’
The Artemis extruder able to address the demand for relatively high-speed 3D printing with flexible filaments. It utilizes an elastic feeding mechanism. This helps prevent issues from developing during high speed operation as well as minimizes pushing or binding that could cause jams. As a result, the Artemis is able to consistently and reliably extrudes these soft materials with the relatively higher speeds.
EIBOS Artemis extruder TPU 85A Test 32min (silent version)
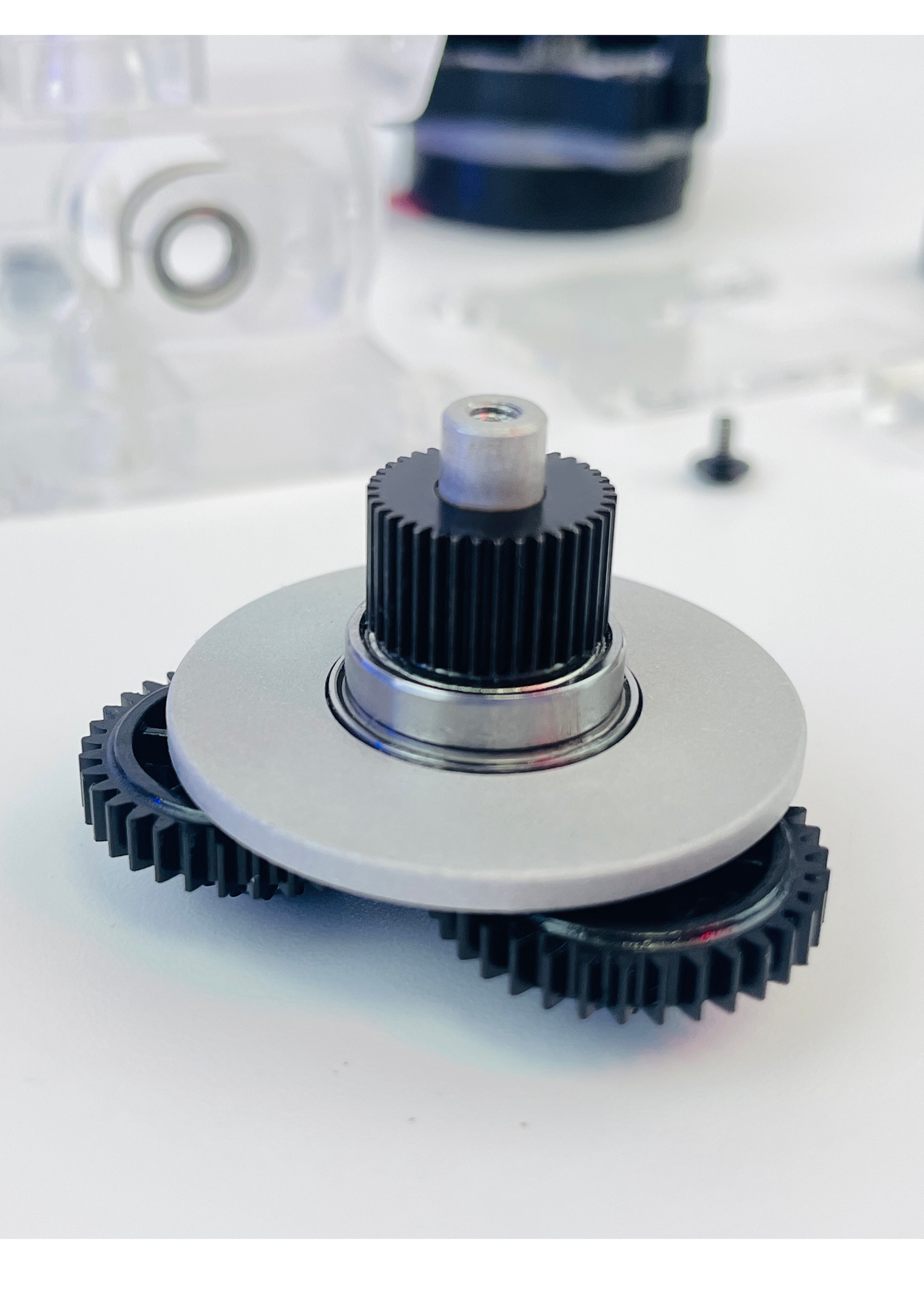
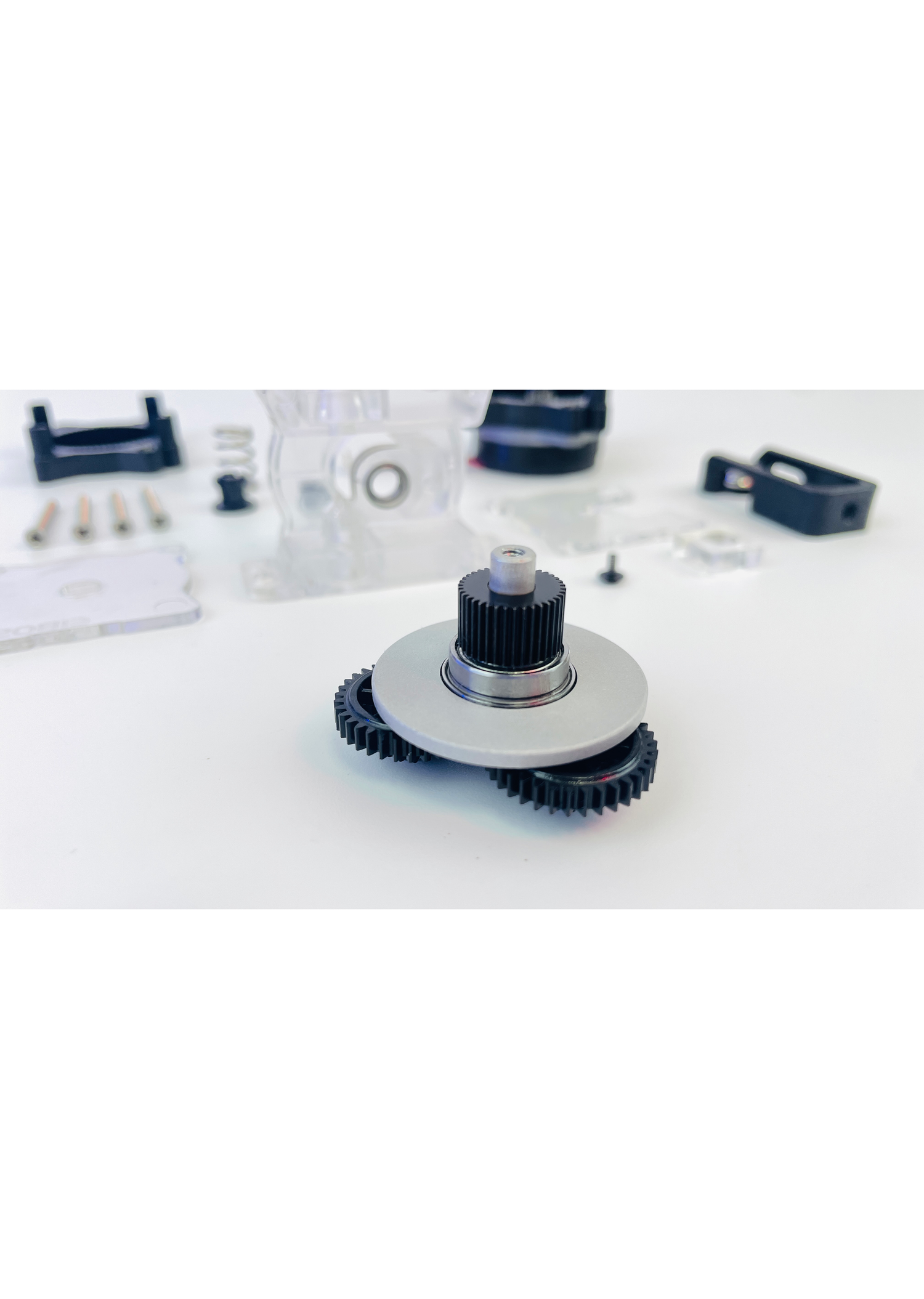
M2 High Alloy Hardened Steel Extruded Gear
'HRC63'
To withstand the demands of high-speed extrusion, the Artemis utilizes a precision-machined M2 high-alloy hardened steel gear. With an outer diameter of 12mm, the gear's through heat treatment process yield exceptional hardness and durability.
First, quenching at 1180°C for 40 minutes induces powerful hardening. Then tempering at 560°C for 120 minutes refines the grain structure. This imparts a ultimate hardness of HRC63 - Much higher than other extrusion gears with a hardness range of 45-55. CNC machining forms sharp tooth tips to properly engage filament. Meanwhile, the grinding process blacks and seals the surface, protecting against corrosion.The resultant gear exhibits tremendous wear resistance through its hardened alloy core and optimized heat treatment.
This allows the Artemis to process high-strength consumables like carbon fiber-infused nylon with greater longevity and consistency versus conventional extruder gears.
Less feeding losses
The Artemis rethinks filament drive mechanisms for high-speed 3D printing. Conventional dual-gear extruders abrade consumables excessively through repeated contact under rapid motion. Metal and plastic debris collect between small gear teeth over time. Left unchecked, eventual clogging disrupts precise feeding. In contrast, the Artemis employs a kinematically simpler single-gear system. Users benefit from reliable performance over more print cycles without risk of premature gear jamming from accumulated filament and gear debris.
Visual transparent window
Most extruders on the market utilize opaque frames and dual gears, hiding the filament feed path from view. Without visibility into the extrusion process, users have limited ability to monitor for early signs of faults. The Artemis addresses this through transparent cover design. with a strong and clear polycarbonate cover, the Artemis offers full exposure of the filament engagement and movement dynamics with the single precision-cut gear. Users can now clearly see the filament entering and exiting while under gear forces. Any accumulation of debris which could prematurely clog extruders in the narrow tooth can be easily found and cleaned. This allows potential issues to be identified and addressed before disrupting prints. With full filament flow visibility, the Artemis empowers users with real-time process observability for preventative maintenance and maximum uptime.